Why Test?
A rim may look perfect at a glance, but builds poorly if details are overlooked. When you build a wheel methodically by hand, you can recognize the quality of work that went into the rim’s construction. Naturally, you want to build the wheel with top quality tools, spokes, and nipples to eliminate as many variables as possible. The wheel should behave predictably as you increase tension and won’t readily develop hops or significant lateral deviations. If the nipple bed has an evenness and is drilled and deburred correctly, the nipples will protrude by the same amount and pull without a harsh angle in relation to the spokes. Rim imperfections are amplified during the wheel building process, so performing regular build tests help us maintain our high-quality standards.
Testing Goals
The wheel building test aims to check the smoothness of the wall and edges, hole drilling angle, reinforcement of the nipple bed, and trueness of the whole wheel.
Test Standard
Hole drilling angle: +/-6°
Nipple bed: no bulge/crack
Wheel trueness: < 0.3mm
Sample Profile
Size | Model | Width/Depth | Rim Weight | Hub | Spokes | Nipples | Rim Condition |
---|---|---|---|---|---|---|---|
700C | WR50 | 32mm/50mm | 473g | DT Swiss 350 | Sapim CX Ray Straightpull | Sapim Polyax aluminum | Trueness test passed. |
Test Facility
A commercial-grade truing stand equipped with lateral and radial runout gauges. 4-sided spoke key or t-handle, and a high-quality tension meter (P&K Lie is a good choice). The wheel builder has 10 years of experience and can recognize some issues tools cannot.
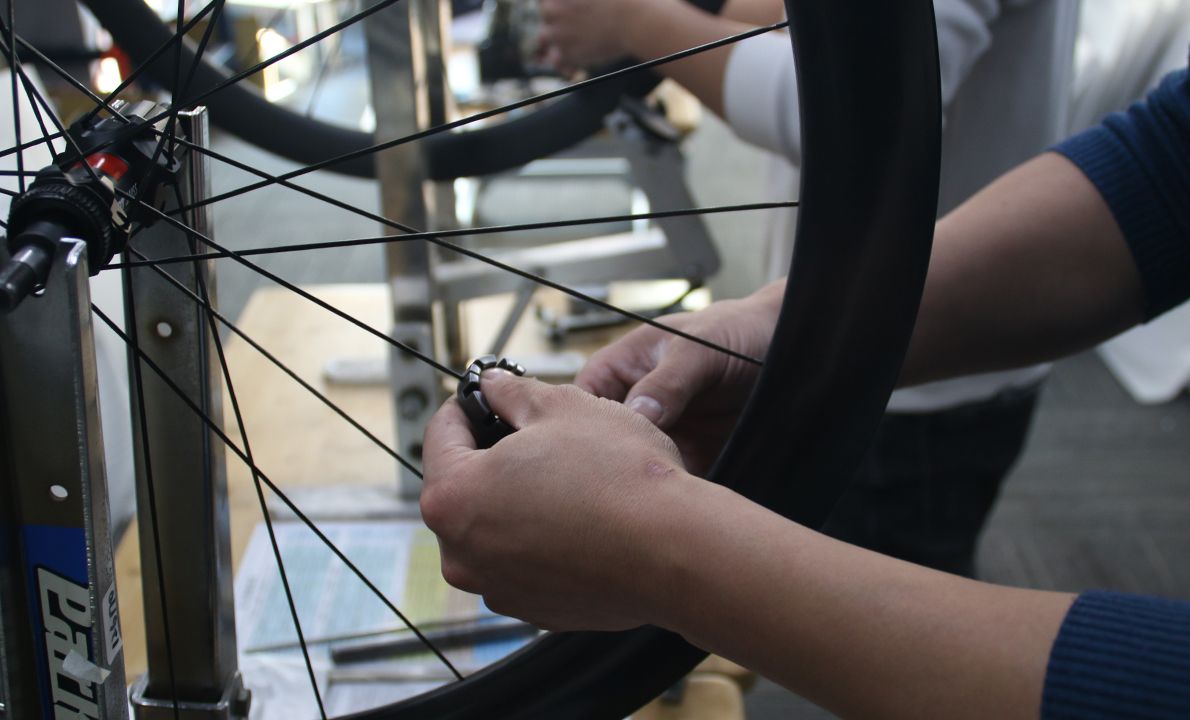
Methodology
- Step 1:Prepare the rim, spokes and nipples, hub, and building tools.
- Step 2:Lace the rim, bring the spokes to even tension, and get the wheel stress relieved.
- Step 3:Inspect the nipple bed area for any bulges or cracks.
- Step 4:True the wheel and inspect its trueness (<0.3mm run-out).
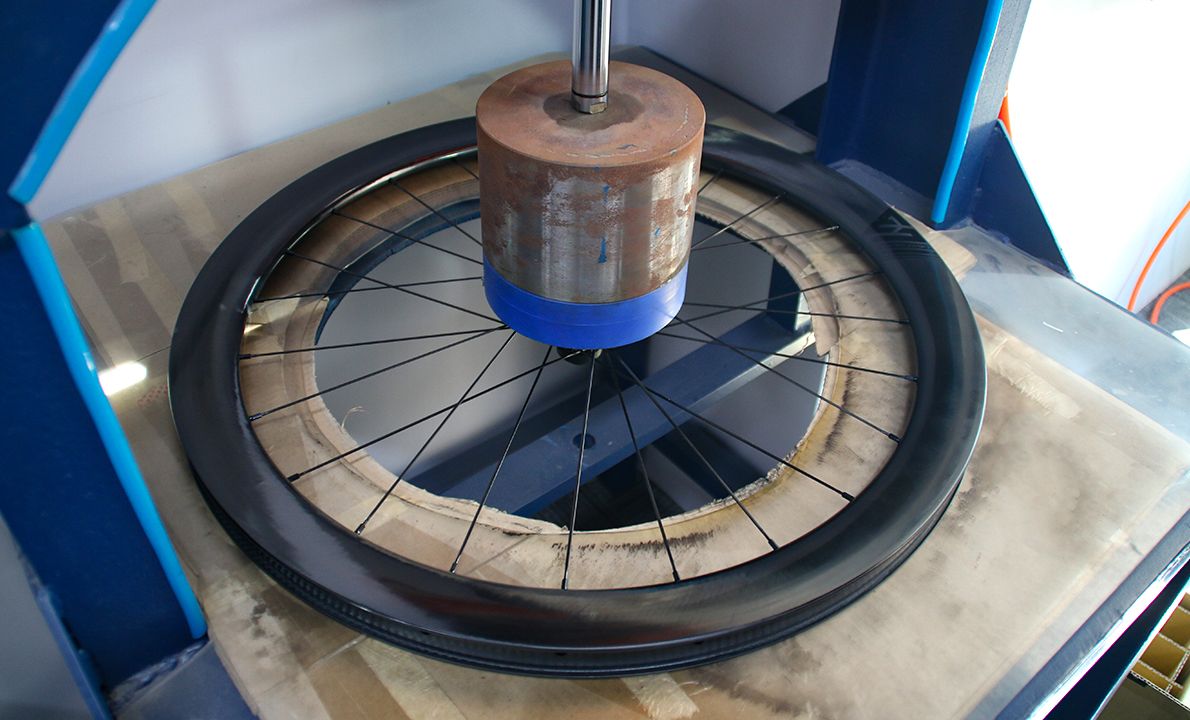
Conclusions
There are no cracks or bulges around the nipple holes, and the nipples fit well into the holes during spoke lacing. Both lateral and radial run-outs of the trued WR50 wheel is around 0.2mm.
© All photos and test data by Light Bicycle
October 24th, 2020 | Light Bicycle
Get in touch
Feel free to leave a comment if you have any questions or suggestions on our products or other issues.

Please leave your name here.
E-mail is required for further contact.
Please enter a message.
We use cookies for a better experience. Learn more.
Your Cookie Preferences
We use cookies to improve your experience on this website. You may choose which types of cookies to allow and change your preferences at any time. Disabling cookies may impact your experience on this website. You can learn more by viewing our Cookie Policy.
-
Cookies required to enable basic website functionality.
-
Cookies used to understand how the website is being used.
-
Cookies that are used to enhance the functionality of the website.
-
Cookies used to deliver advertising that is more relevant to your interests.
Aceept All Cookies
Save Preferences
Reject All Cookies
Save Preferences
Reject All Cookies
Accept All Cookies