How do Recon rims come out?
As a matter of fact, more and more people choose carbon fiber over aluminum due to the higher tensile strength, tensile stiffness, and the excellent weight-to-stiffness ratio. Different carbon fiber has a different weight-to-stiffness ratio. LightBicycle chooses different fiber on different models, layup layers and different parts to make the rim light without losing stiffness
BASIC TECHNOLOGIES
Most of the basic technologies are also applied to Pro series rims.
bft
Burp Free Technology
APE
Anti Pinch-flats Edge
HBT
Hookless Bead Technology
arp
Asymmetric Rim Profile
opl
One-piece layup Technology
hqm
Only the highest quality material is used
NrP
No Rim bed Patching
sab
Specially design Air Bladder
NrI
No residue inside the rim
NCr
No Curing Carbon Ring
era
Environmentally-friendly
mpt
Molding Pulsation Technology
ccc
Cooling Cycle Completion
adt
Angle Drilling Technology
sdh
Smooth drilling holes (CNC)
fpp
Flow Production Process
vcf
Visualized Carbon Fiber

/ Burp Free Technology
All Light Bicycle rims are tubeless compatible. The bump on the rim bed helps to create a buffer during tire inflation, making the mounting process easier. When the tire is mounted, the raised portion reinforces the tire bead, making it harder to “burp” or fall back into the drop channel.
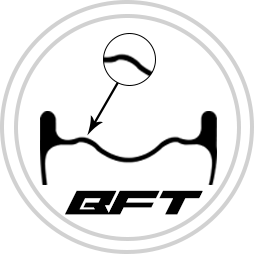
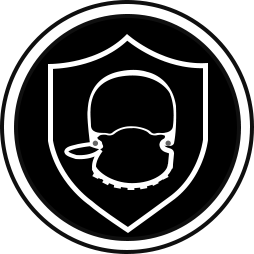

/ Anti Pinch-flats Edge
The rounded edge makes tire installation easier and offers increased support during hard cornering with a softer edge and larger surface area.

/ Hookless Bead Technology
Our hookless design has consistent carbon compaction and there are no voids in the layup, providing the rim with a greater ability to withstand sharp impacts.
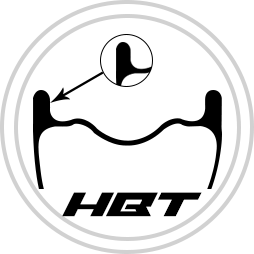
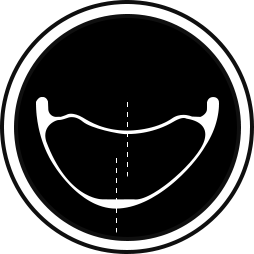

/ Asymmetric Rim Profile
At 2012, we invented one of the first asymmetric mountain bike rims in the industry, furthermore, we’ve optimized the asymmetric profile that maintains the outright impact performance of asymmetric design but enjoys the benefits of offset spoke holes. This design significantly equalizes spoke tension between drive and non-drive spokes which results in a stronger wheel build that would maintain true longer.

/ Only the highest quality material is used
Carbon rims are complex shapes that require the best material available in
order to produce a top quality product. Toray is a leading global
manufacturer of carbon fiber and produces some of the industry’s most
consistent products. The bulk of our rims are made with Toray’s
unidirectional (UD) fiber, and we offer an optional woven 3k or 12k top
layer. TORAYCA T700S is a mainstay in all of our rims, and we use T800S in
some models to help reduce weight or increase stiffness in particular areas.
Why not T1000?
Many people ask why Light Bicycle doesn’t use T1000G. not using T1000G
that beats T800S at strand strength? True, T1000 has a higher strand
strength compared to T700 & T800, but it is primarily used in military or
aircraft manufacturing, costing roughly four times in price. We are also not
able to secure enough of the material to use effectively.
Material Preparation.
The carbon fiber is impregnated with resin before it is laid in molds. This is
known as a prepreg. The engineering team determines the resin ratio, size,
shape, type, thickness and angle of every piece of carbon fiber in a given rim.
The layup schedule is critical to the performance and longevity of the rim.
Rolls of prepreg are stored in a climate-controlled room, and released in
small batches for cutting during a production run.
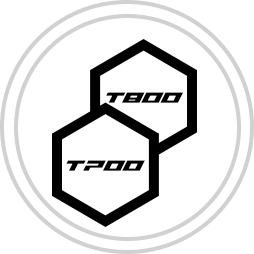
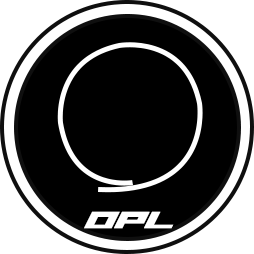

/ One-piece layup Technology
After the material is cut to size, it is delivered to the layup room. The layup
workers are extremely skillful and our most experienced workers. The
layup is performed by hand and is strategically built up in many layers.
Every piece of prepreg is carefully oriented in a pre-formed core with the
appropriate overlap.
We developed a one-piece layup design to increase continuity and reduce
the number of overlapping seams. We have upgraded our equipment to
handle large accurate cuts, and the end result is a rim that is not only
stronger but also lighter.

/ No Rim bed Patching
Other factories pull out the core used in the layup process through a large hole cut into the rim bed, which is then patched. Under this process, a worker cannot accurately match the fiber orientation of the layers, and rim continuity is sacrificed. Wheel builders will notice that rims with this patching behave erratically during wheel tensioning. Light Bicycle builds differently. Our rims do not have any patching as we have a special process for avoiding this.
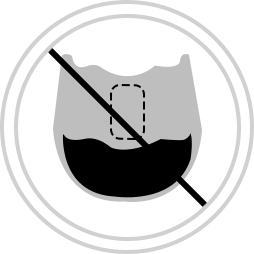
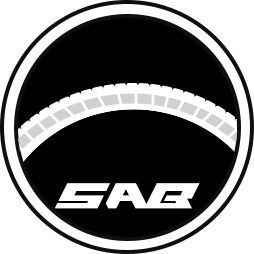

/ Specially designed Air Bladder
Air bladders are inflated inside the rims during the molding process, but not all air bladders are created equal. We have numerous air bladders designed specifically for particular rim shapes, built thinner and of a higher quality than most factories. The thinner material can extend into tight areas of the rim, creating smoother walls and a more consistent nipple bed. The strict handling and storage conditions of our air bladders have significantly improved the interior of our rims.

/ NO residue inside the rim
Other rim manufacturers sell their rims with voids in the layup and the air bladders still inside. Although it’s faster to leave them in, we carefully remove the air bladder so that no material is left behind. Every gram counts!
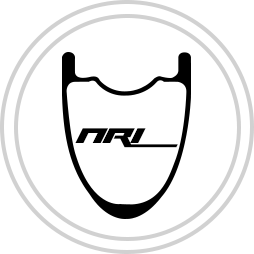
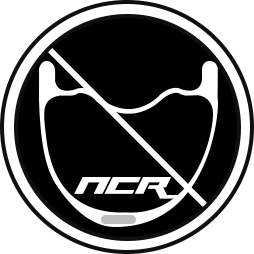

/ No Curing Carbon Ring
Some manufacturers use a curing ring (some call it a carbon strip) for a more even, reinforced nipple bed. The challenge with this practice is the rim must undergo a double molding process. The curing ring reacts differently compared to the rest of the rim, ultimately leading to a weaker structure. Light Bicycle was one of the pioneers to eliminate this process years ago, and yet quite a few companies are still manufacturing with the curing ring

/ Environmentally-friendly Release Agent
A release agent is applied to the mold to make it easier to remove the rims.
The most common release agent used in carbon rim manufacturing is oily and
mixed with a small amount of wax. There will be some residue on the rim
surface after it comes out of the mold, so wet-sanding is used for removal.
This isn’t an option for our Pro rims.
Desiring an effective mold release agent that was also as green as possible
proved to be a challenge. We opted for the more expensive Henkel and
Chem-Trend, and based on the product’s performance we stand by our
decision. This non-transfer type release agent forms microfilm by chemically
bonding with the surface of the mold. The film remains stable at high heat,
withstanding temperatures up to 400 ° C. After the molding process, the
release agent flashes off so no sanding is required.
The application of the release agent is critical, we need to warm the mold up
to a certain temperature in order to apply it, and it needs to be spread very
evenly. We deploy a heat-sensitive camera to check our work.
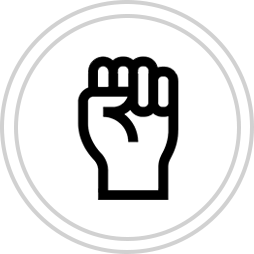
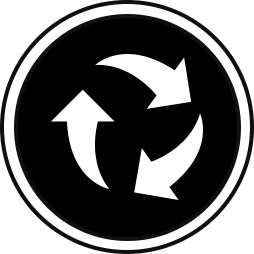

/ Molding Pulsation Technology
The molding pulsation refers to the dynamic control of air pressure to reach
a balanced value that matches the resin flow. Air pressure, oil pressure and
temperature must be adjusted frequently as the resin discharge changes
during the entire molding process.
What does it do?
1. Avoids problems like over-discharged resin, air wrap on the rim surface, etc.
2. Makes the binding force between carbon layers stronger, increasing the fatigue life of the rim.

/ Cooling Cycle Completion
Our rims are left in the mold until the cooling cycle is complete. Most factories will remove the rim after it’s cured so that another rim can be put into production. Although slower, we find our method yields a more dimensionally accurate product.
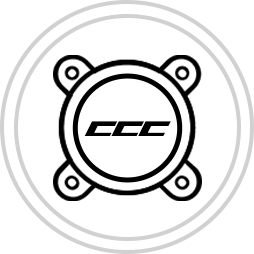
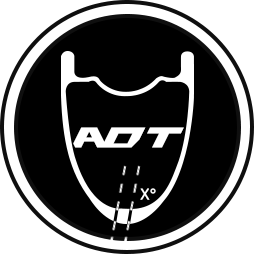

/ Angle Drilling Technology
The spoke holes of all Light Bicycle rims are drilled with a certain angle (axial direction and radial direction) to reduce the stress of the nipple, rim, and spoke interface. You can request a customized drilling pattern if you have a unique wheel build.

/ Smooth drilling holes (CNC)
Our rims are drilled with a CNC machine. Each hole is inspected to ensure they are clean and free of burrs. The drilling speed and temperature is adjusted as the bit wears, and we inspect after every 60 holes to ensure consistent quality.
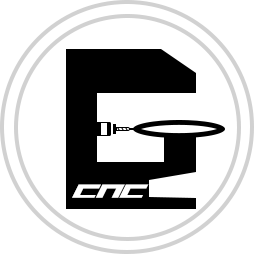
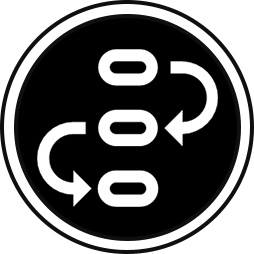

/ Flow Production Process
Light Bicycle is not a large production facility - we are experts in smaller custom orders. Yes, we produce a lot of rims, but our process is much different from “the big guys”. Traditionally, rims are ordered in large batches and travel through the various production cycles within that big batch. This means that rims are often sitting waiting for others in their group to be completed before the next process begins. During this time they can deform because they are not cured, and risk contamination. The productivity and cost is lower with this method, but the quality suffers.
With our process, the rims don’t stop moving once the process starts. Once a rim enters the production cycle, it moves swiftly between processes and is not left waiting for other rims in its “batch”. When a rim comes out of pre-mold, the final mold is already prepped and ready. Light Bicycle first started as a direct to consumer business and had to master the art of handling custom orders. The dynamic coordination of our production team took years of refinement, and now we’re able to handle thousands of rims each month with hundreds of variations that would cripple most production lines.

/ Visualized Carbon Fiber
Our non-pro series of rims are wet sanded and then a thin layer of clear coating is applied to create a near-flawless finish. You can see the fiber orientation underneath the clear coat. Unlike some competitors, we do not add any black pigment or try to hide any defects. Only minor aesthetic imperfections barely visible to the naked eye are allowed to pass through QC.
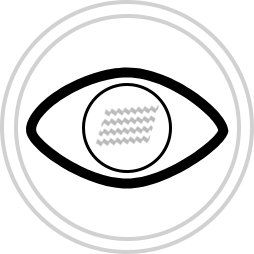
Quality Control Process
Each of our rims is submitted to rigorous QC checks throughout the entire manufacturing process: after each production process, a QC check follows. In this way, we note and correct irregularities before a rim continue on to the next step. Every rim is weighed and carefully inspected for discrepancies such as material contamination and visual defects.
You might notice that our Pro series uses a varying manufacturing process, learn more about Pro series Tech here.
WARRANTY OPTIONS
Whether your tough on wheels or have never cracked rim, our new warranty gives you the opportunity to get the coverage you need and avoid overpaying for what you don’t want. Our Recon line of rims comes standard with 3-year Warranty from the date of purchase.
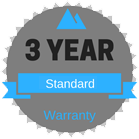
RIM LIST
3-year Warranty from the date of purchase.
Rim model | Outer Width | Depth | Discipline | Weight(+/-15g) | Price(each) | Explore |
---|---|---|---|---|---|---|
29er-RM29C06 | 27mm | 24mm | Cross Country | 280g flyweight 360g standard |
USD 158 USD 143 |
Buy
Section View
|
29er-RM29C19 | 30mm | 25mm | Cross Country | 395g | USD 153 |
Buy
Section View
|
29er-RM29T01 | 27mm | 24mm | Cross Country | 320g | USD 162 |
Buy
Section View
|
29er-RM29C19 | 30mm | 25mm | All Mountain |
395g | USD 153 |
Buy
Section View
|
29er-RM29C07 | 35mm | 25.5mm | All Mountain Enduro/DH |
420g 465g |
USD 180 USD 185 |
Buy
Section View
|
29er-AM928 | 34mm | 28mm | All Mountain | 430g | USD 154 |
Buy
Section View
|
29er-EN928 | 34mm | 28mm | Enduro/DH | 480g | USD 159 |
Buy
Section View
|
29er-AM933 | 39mm | 28mm | All Mountain | 460g | USD 163 |
Buy
Section View
|
29er-EN933 | 39mm | 28mm | Enduro/DH E-bike |
510g | USD 168 |
Buy
Section View
|
29er-RM29C14 | 38mm | 32mm | All Mountain Cross Country Enduro/DH |
465g 515g |
USD 185 USD 190 |
Buy
Section View
|
29er-RM29C15 | 50mm | 22.5mm | Plus | 490g | USD 173 |
Buy
Section View
|
650B-RM650BC09 | 27mm | 24mm | Cross Country | 270g flyweight 320g standard |
USD 158 USD 143 |
Buy
Section View
|
650B-AM724 | 30mm | 24mm | All Mountain Cross Country |
385g | USD 154 |
Buy
Section View
|
650B-RM650BC05 | 35mm | 25.5mm | All Mountain Enduro/DH |
400g 455g |
USD 175 USD 180 |
Buy
Section View
|
650B-AM728 | 34mm | 28mm | All Mountain Cross Country |
410g | USD 154 |
Buy
Section View
|
650B-EN728 | 34mm | 28mm | Enduro/DH | 460g | USD 159 |
Buy
Section View
|
650B-RM650BC13 | 38mm | 32mm |
All Mountain Cross Country Enduro/DH |
455g 505g |
USD 180 USD 185 |
Buy
Section View
|
650B-AM733 | 40mm | 31.5mm |
All Mountain Cross Country |
460g | USD 163 |
Buy
Section View
|
650B-EN733 | 40mm | 31.5mm |
All Mountain E-bike |
510g | USD 168 |
Buy
Section View
|
650B-RM650BC14 | 50mm | 22.5mm | Plus | 450g | USD 173 |
Buy
Section View
|
650B-AM740 | 46mm | 28mm | Plus | 480g | USD 164 |
Buy
Section View
|
650B-EN740 | 46mm | 28mm |
Enduro/DH E-bike |
530g | USD 169 |
Buy
Section View
|
26er-RM26C02 | 30mm | 22mm |
All Mountain Cross Country |
360g | USD 149 |
Buy
Section View
|
26er-RM26C03 | 33mm | 30mm |
All Mountain Cross Country Enduro/DH |
385g 430g |
USD 153 USD 158 |
Buy
Section View
|
26er-RM26C05 | 38mm | 32mm |
All Mountain Enduro/DH |
420g 485g |
USD 154 USD 159 |
Buy
Section View
|
26er-RM26C06 | 46mm | 25mm | Plus | 440g | USD 164 |
Buy
Section View
|
We use cookies for a better experience. Learn more.
Your Cookie Preferences
We use cookies to improve your experience on this website. You may choose which types of cookies to allow and change your preferences at any time. Disabling cookies may impact your experience on this website. You can learn more by viewing our Cookie Policy.
-
Cookies required to enable basic website functionality.
-
Cookies used to understand how the website is being used.
-
Cookies that are used to enhance the functionality of the website.
-
Cookies used to deliver advertising that is more relevant to your interests.
Aceept All Cookies
Save Preferences
Reject All Cookies
Save Preferences
Reject All Cookies
Accept All Cookies