What Is Falcon Pro All About?
It is about making road rims that stand the test of time via a more eco-friendly manufacturing process. Two years ago, this ambitious project kicked off. We streamlined the production line from the very first step: material preparation. Thinner and lighter material allows us to form more layers - rim strength is boosted without weight penalty.
Falcon Pro rims come out of the mold as a finished product, and we named this paintless innovation “BlackTek”. No post-production work is required as the out-of-mold finish is smooth and tough. With the naked eye, you can see through the raw finish to the UD fibers beneath. Every Falcon Pro rim has a special fiber pattern which delivers your wheels a unique look.
The Features
- 20% Stronger
- More Impact Resistant
- Highly Scratch-Resistant
- More Environmentally Friendly
- Optional Lifetime Warranty
- Paintless Finish
- All Road Use
- Optional lightweight “Flyweight” model available
Pro Technologies
What makes Falcon Pro pro?
HTB
High TG Rim Brake Track
GGB
Grooved Graphene Brake Track
BKT
Black Tek
IPC
Irregular Profile Cutting
SCL
Stepwise Cross-Link
TLO
Thinner Laminates Orientation-Optimized
SWT
Smooth Wall Technology
ACD
Aviation Class CNC Drills
XFP
X-Flow Profile
ERA
Environmentally-friendly Release Agent
ART
AeroTech
DSB
Dynamic Speed Balancer
TCT
Tubeless Compatible Technology
FTI
Fast Tire Installation
WSR
Weight-to-stiffness ratio
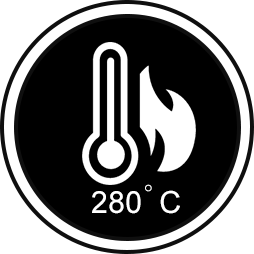

/ High TG Rim Brake Track
Our resin system and construction method, combined with the 3k rim track, withstands over 280°C, dissipates heat, and lowers rim temperatures faster between braking efforts. Gain confidence inspiring brake performance on the steepest descents and wet conditions with our matching brake pads.

/ Grooved Graphene Brake Track
Our graphene version of the High TG brake track has even greater resistance to overheating with improved heat dissipation and reduced temperature accumulation during heavy braking. The grooved track helps evacuate trapped moisture between pad and rim in the wet and brings more resistance when conditions are dry, so less force at the lever is required.
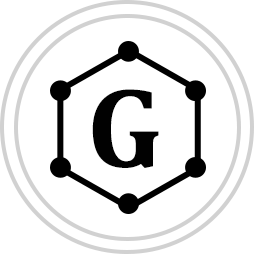
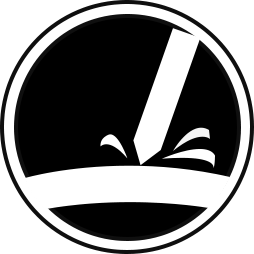

/ Black Tek
Rims featuring BlackTek come out of the molds as a finished product. The factory finish preserves the outer layer of resin and the carbon is never disturbed after the curing cycle is completed. This is the hardest wearing finish we have ever produced.

/ Irregular Profile Cutting
To ensure the strips of prepreg fit the curves of rims, we carefully stretch the material in length or width to achieve an optimal fit without harming the consistency of the UD fibers (too much force will create a weak point on the rim). For some complex shapes, we have an automated cutting process where the material is cut with the curves, grooves, and hooks of a certain rim model in mind. The results? Fiber layup can be done with more accuracy and efficiency, and the product comes with increased overall strength.
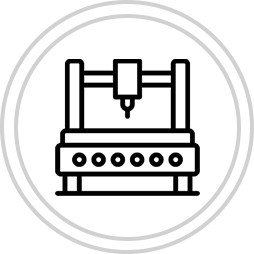
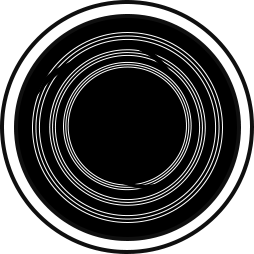

/ Stepwise Cross-Link
Traditionally, several laminates are piled with the edges aligning to form a layer, with a layer applied across the mold end to end, forming one overlap point per layer. The overlapping area is a bit thicker and heavier than the rest, which could leave the rim unbalanced. We stagger the seams so they never directly overlap another seam. The edges are stepped, or overlapped by 2mm and are unnoticeable once the rim is complete.

/ Thinner Laminates Orientation-Optimized
We use thinner and lighter materials that allow us to form more laminates per layer, achieving stronger cross-linking reactions. Every laminate is ultra-thin, and the extremely smooth unidirectional (UD) plies create a mechanical performance gain. The thinner material is usually twice as expensive. There are more square meters used in each rim, and the layup takes much longer. The advantage is weight reduction and the ability to fine-tune the characteristics of the rim without sacrificing strength or stiffness.
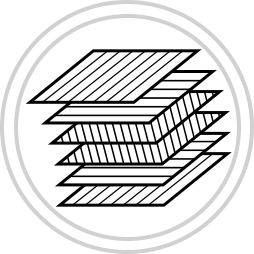
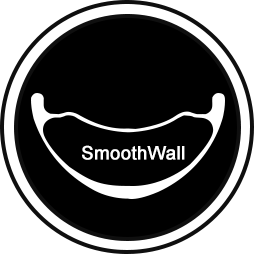

/ Smooth Wall Technology
We’ve developed a special air bladder material that follows the inner contours of our rims. Coupled with our three-dimensionally shaped air duct, the inner wall of the rim is smoother, lighter, and without wrinkles. The bladder is removed through the valve hole so no patching is required.

/ Aviation Class CNC Drills
No tear out! Our Pro rims are drilled with aviation-grade CNC machines specifically designed for drilling through advanced composites. The bits have a unique cutting edge that make extremely clean holes. Each hole is inspected to ensure they are free of burrs. The drilling speed and temperature are adjusted as the bit wears, and the bit is inspected after every 60 holes. Competitors use more common high-speed bits which heat the holes and often leave scorch marks. It is not uncommon to see some delamination in other carbon rims due to their inferior drilling process.
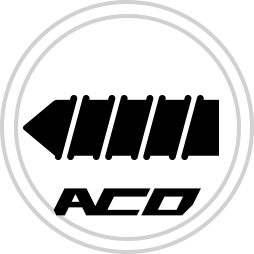
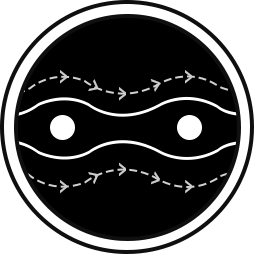
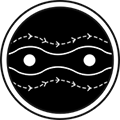
/ X-Flow Profile
The wave style X-Flow rims feature a reduced aero drag, boosted lateral stiffness, and greater impact resistance, compared to our traditional design road rims. We sent several R and AR counterparts along with the newly designed X-Flow rims for comparison, to a third-party testing institute using Computational Fluid Dynamics (CFD). Based on the samples tested, removing crosswinds from the equation for a fair comparison, the X-Flow rims perform the best.

/ Environmentally-friendly Release Agent
A release agent is applied on the mold to increase ease of rim removal. The most common
release agent used in carbon rim manufacturing is oily and mixed with a small amount of
wax. There will be some residue on the rim surface after it comes out of the mold,
so wet-sanding is used. This isn’t an option for our Pro rims.
Finding an effective mold release agent that was also as green as possible proved to be a challenge.
We opted for the more expensive Henkel and Chem-Trend, and based on the product’s performance we stand by our decision.
This non-transfer type release agent forms microfilm by chemically bonding with the surface of the mold. The film remains stable at high heat,
withstanding temperatures up to 400°C. After the molding process, the release agent flashes off so no sanding is required.
The application of the release agent is critical: the mold must be warmed to a specific temperature for application,
and it needs to be spread very evenly. We use a heat-sensitive camera to check our work.
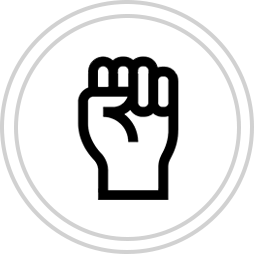


/ AeroTech
The greatest carbon fibre upgrade appeal is the aerodynamic advantage over a box-section aluminum rim.
Our aerodynamic profile reduces drag significantly as proven by 3rd party studies like Hambini Engineering.
If you’re racing, whether against the clock in a time trial or in a road race, deep dish carbon wheels will make
a noticeable difference at higher speeds without the weight disadvantage of alloy wheels.
We have a host of modern wider road rims available. When the rim width is closer to the tire's actual width,
the airflow tends to be smoother than the lightbulb shape of a wide tire-narrow rim.

/ Dynamic Speed Balancer
In the quest to make our rims as light as possible, adding weights to achieve balance on our wheels is unacceptable. We use Dynamic Speed Balance (DSB™) on our rim layup design, a unique bicycle wheel balance system that doesn’t require added weights or gadgets to achieve perfect rotational wheel balance.The shaking reduces at least 90% compared to rims that don’t feature a weight balance system.
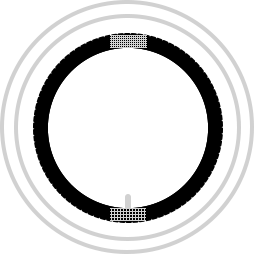
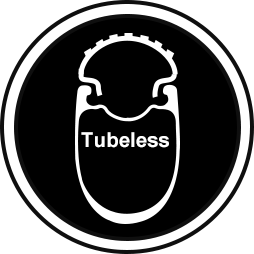

/ Tubeless Compatible Technology
All of our rims are tubeless compatible with bead seat retention. In most cases a floor pump is needed to seal our rims. The bead shape, bead seat and outer diameter is tailored according to each rim width in order to achieve the best fit. Tubeless (no tube) systems are designed to run at lower pressures than tube systems without any negative effects. Lower rolling resistance, decreased rotational weight and flat resistance are all significant improvements.

/ Fast Tire Installation
Our deeper tire bead channel provides easy tire mounting and dismounting. We shipped our rims to Schwalbe for a tubeless easy fitting test, and the results were great! Most of our Falcon rims are easy to install by tire lever, some of them even relatively easy to install only by hand. You can check out the page at Schwalbe's official site.
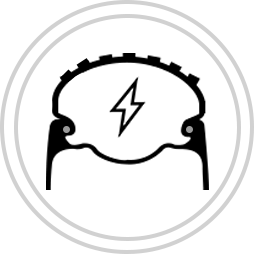
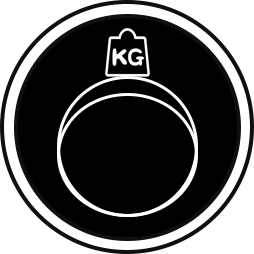

/ Weight-to-stiffness ratio
We use thinner pre-pregs for better control over the layup. In an area that typically has 9 different layers, we might have 12, but the thickness is the same. More layers means that when we change the orientation between layers it has a greater impact on the rim’s stiffness. Using a wider range of material allows us to create lighter rims without losing desired stiffness.
WARRANTY OPTIONS
Whether you‘re tough on wheels or have never cracked a rim, our new warranty gives you the opportunity to get the coverage you need and avoid overpaying for what you don’t want. Our Falcon Pro line of rims come standard with our Pro 5-year Warranty against manufacturer's defects and, for the first time ever, with the option to upgrade this standard warranty to our Premium Lifetime Warranty.
RIM LIST
5-year or an optional lifetime warranty from the date of purchase.
Model | External Width | Depth | Discipline | Weight (+/-15g) | Price (each) | Explore |
---|---|---|---|---|---|---|
AR35 disc | 28mm | 35mm | Road/CX/Gravel |
Standard 410g Flyweight 350g |
Standard $239 Flyweight $251 |
Buy
Section View
|
WR40 disc | 32mm | 40mm | CX/Gravel |
Standard 440g Flyweight 400g |
Standard $269 Flyweight $281 |
Buy
Section View
|
AR45 disc | 28mm | 45mm | Road/CX/Gravel |
Standard 460g Flyweight 380g |
Standard $249 Flyweight $261 |
Buy
Section View
|
WR38 disc | 32mm | 38mm | CX/Gravel |
Standard 440g Flyweight 385g |
Standard $239 Flyweight $251 |
Buy
Section View
Section View
|
WR50 disc | 32mm | 50mm | CX/Gravel |
Standard 470g Flyweight 410g |
Standard $259 Flyweight $271 |
Buy
Section View
Section View
|
WR35 650b disc | 32mm | 35mm | CX/Gravel | Standard 370g | Standard $259 |
Buy
Section View
Section View
|
AR55 disc | 28mm | 55mm | Road/CX/Gravel |
Standard 480g Flyweight 420g |
Standard $259 Flyweight $271 |
Buy
Section View
Section View
|
AR375 disc | 28mm | 37.5mm | Road/CX/Gravel |
Standard 440g Flyweight 390g |
Standard $269 Flyweight $281 |
Buy
Section View
|
AR465 disc | 28mm | 46.5mm | Road/CX/Gravel |
Standard 460g Flyweight 410g |
Standard $279 Flyweight $291 |
Buy
Section View
|
AR375 | 28mm | 37.5mm | Road/CX/Gravel |
Standard 450g Flyweight 410g |
Standard $269 Flyweight $281 |
Buy
Section View
|
AR465 | 28mm | 46.5mm | Road/CX/Gravel |
Standard 470g Flyweight 430g |
Standard $279 Flyweight $291 |
Buy
Section View
|
We use cookies for a better experience. Learn more.
Your Cookie Preferences
We use cookies to improve your experience on this website. You may choose which types of cookies to allow and change your preferences at any time. Disabling cookies may impact your experience on this website. You can learn more by viewing our Cookie Policy.
-
Cookies required to enable basic website functionality.
-
Cookies used to understand how the website is being used.
-
Cookies that are used to enhance the functionality of the website.
-
Cookies used to deliver advertising that is more relevant to your interests.
Aceept All Cookies
Save Preferences
Reject All Cookies
Save Preferences
Reject All Cookies
Accept All Cookies